Integrating heating solutions during construction can enhance energy efficiency and sustainability. This guide outlines steps to ensure effective integration of heating systems, focusing on planning, installation, and testing. By considering heating systems early in the construction process, builders can optimize resource use and reduce long-term operational costs.
Pre-construction planning
Effective integration of heating solutions begins with pre-construction planning. Architects and engineers assess the building’s thermal mass, selecting materials like phase change materials (PCM) to enhance thermal inertia. These materials help regulate indoor temperatures, reducing the need for artificial heating. For instance, incorporating high-density materials in walls and floors can store heat during the day and release it when temperatures drop. Additionally, careful orientation of the building and window placement can maximize natural heat gain.
Selecting a suitable heating system based on building size, occupancy, and climate is necessary. In colder regions, a combination of heat pumps and radiant floor heating might be appropriate. Advanced HVAC systems, like those provided by Cairox, can improve efficiency. Cairox offers products that integrate renewable energy sources, such as solar thermal systems, to reduce carbon footprints. Consulting with HVAC specialists during this phase can help tailor systems to specific project requirements.
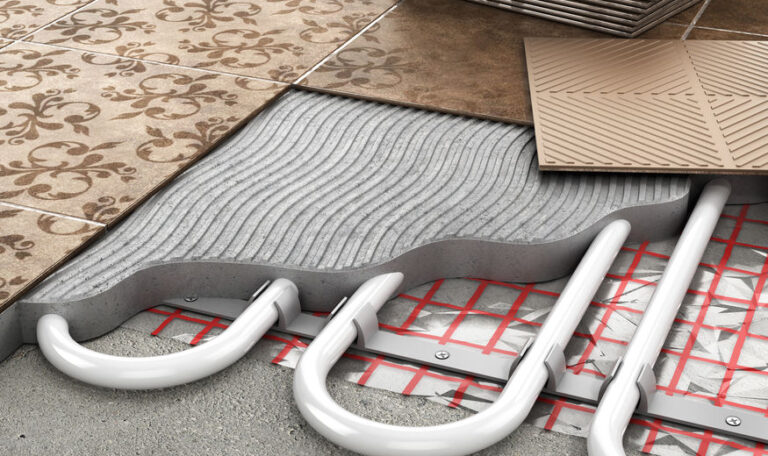
Installation during construction
Proper installation during construction is key to ensuring the heating system functions efficiently. Following manufacturer’s guidelines and ensuring correct component sizing and placement is necessary. Correct radiator placement and appropriate boiler sizing contribute to system effectiveness. Installing insulation around pipes and ducts can prevent heat loss and improve overall system efficiency. Furthermore, selecting high-efficiency components can provide energy savings over the life of the building.
Coordination with other trades, such as electrical and plumbing, helps avoid conflicts or delays. Visual aids, like diagrams, can be useful for explaining the installation process to the construction team. Regular inspections during this phase can help identify potential issues early. Ensuring that all installations comply with safety standards is also essential to prevent future hazards.
Post-construction testing
After installation, thorough testing is necessary to verify that the heating system meets regulatory and operational standards. This includes checking system functionality, making adjustments as needed, and ensuring compliance with building codes and regulations like RE 2020 in France. Testing may involve balancing the system to ensure even heat distribution and verifying that control systems operate correctly. It’s also an opportunity to train building managers or owners on system operation for optimal use.
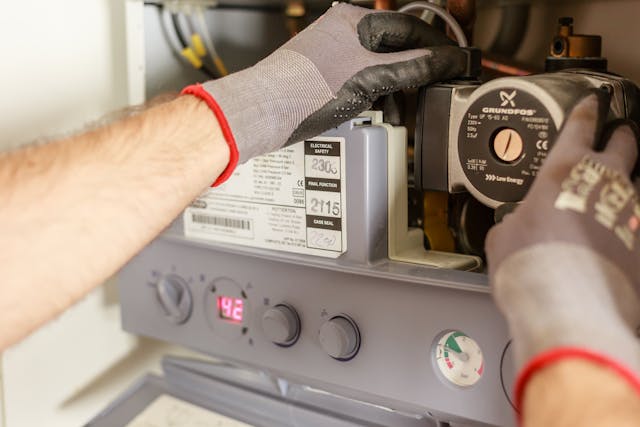
Regular maintenance checks are important to keep the system efficient and compliant over its lifespan. These checks can help prevent issues and extend the system’s operational life. Scheduling routine inspections can detect wear and tear before it leads to significant problems. Utilizing data from smart sensors can also provide insights into system performance over time.
Final thoughts
Integrating heating solutions during construction requires planning, precise installation, and comprehensive testing. By focusing on energy efficiency and sustainability, and using advanced systems, construction professionals can create buildings that are comfortable and environmentally responsible. Embracing innovative technologies and sustainable practices not only benefits the environment but can also lead to cost savings for building owners.